scanningman
Newbie
Hi, my good old scanner has some problem after i wanted to use it after 3 years of rest. First problem was that it doest want to calibrate the white balance, ok, i know what need to do.. replace the halogen bulb, check contacts, adjust pmt gain etc... BUT i think the main problem is, that the aperture ia started to fail on some settings, and now at every setting.
First was a strange sizzling/grinding sound from the aperture motor. I made an aperture calibration with the service program, it was successful, but after a short time it is bad again. On some aperture/resolution setting the preview is totally black, so it is sure that the aperture plate is blocking the light path.
I think the problem with the white calibration is probably failed due to this reason.. and there ia some other noise(clicking sound) what is coming from the right side of scanner, below the light tube. First i thought that only the aperture motor gone wrong, but it is working, moving the aperture, but can't find the right position, and when it reach the 6(largest aperture), starting to make the grinding noise.
Even when the program calculating the white balance, after the procedure is finished, and the drum moving back to parking position, sometimes it stuck at half route and the servo motor makes a strange sound.
I think it will be some electrical/ controller problem...
Any tip?
First was a strange sizzling/grinding sound from the aperture motor. I made an aperture calibration with the service program, it was successful, but after a short time it is bad again. On some aperture/resolution setting the preview is totally black, so it is sure that the aperture plate is blocking the light path.
I think the problem with the white calibration is probably failed due to this reason.. and there ia some other noise(clicking sound) what is coming from the right side of scanner, below the light tube. First i thought that only the aperture motor gone wrong, but it is working, moving the aperture, but can't find the right position, and when it reach the 6(largest aperture), starting to make the grinding noise.
Even when the program calculating the white balance, after the procedure is finished, and the drum moving back to parking position, sometimes it stuck at half route and the servo motor makes a strange sound.
I think it will be some electrical/ controller problem...
Any tip?
monkeyfist
Established
Might be just a case of some old lubricant, the aperture motor is not particularly powerful. Cleaning the mechanism might solve it.Hi, my good old scanner has some problem after i wanted to use it after 3 years of rest. First problem was that it doest want to calibrate the white balance, ok, i know what need to do.. replace the halogen bulb, check contacts, adjust pmt gain etc... BUT i think the main problem is, that the aperture ia started to fail on some settings, and now at every setting.
First was a strange sizzling/grinding sound from the aperture motor. I made an aperture calibration with the service program, it was successful, but after a short time it is bad again. On some aperture/resolution setting the preview is totally black, so it is sure that the aperture plate is blocking the light path.
I think the problem with the white calibration is probably failed due to this reason.. and there ia some other noise(clicking sound) what is coming from the right side of scanner, below the light tube. First i thought that only the aperture motor gone wrong, but it is working, moving the aperture, but can't find the right position, and when it reach the 6(largest aperture), starting to make the grinding noise.
Even when the program calculating the white balance, after the procedure is finished, and the drum moving back to parking position, sometimes it stuck at half route and the servo motor makes a strange sound.
I think it will be some electrical/ controller problem...
Any tip?
Drum getting stuck and stepper motor making a sound, kinda just implies that it got stuck. When stepper motors get stuck they do produce a weird noise, and their torque basically dies completely. So they can't start moving again unless helped a bit.
This might simply also be a case of old lubricants, you might want to clean all the bars that have linear bearings on winch the drum moves. And maybe also the leadscrew or apply some light lubrification on all of these friction surfaces to make sure it moves nice and freely.
scanningman
Newbie
It seems the most problematic part of the scanner is actually the relay board, i am hearig the clicking sound more and more often . The system is collapsing even after some aperture calibration, wb calibration, or a simple scan/preview.Might be just a case of some old lubricant, the aperture motor is not particularly powerful. Cleaning the mechanism might solve it.
Drum getting stuck and stepper motor making a sound, kinda just implies that it got stuck. When stepper motors get stuck they do produce a weird noise, and their torque basically dies completely. So they can't start moving again unless helped a bit.
This might simply also be a case of old lubricants, you might want to clean all the bars that have linear bearings on winch the drum moves. And maybe also the leadscrew or apply some light lubrification on all of these friction surfaces to make sure it moves nice and freely.
maybe the roots of all problem is the driver board/power supply.
what do you think?
xanderrrrrr
Newbie
Hey guys, not sure if anyone has experience with the "hidden service menu" items in the service program... here's what I've found:
Scanmate 5000 Secret Service Menu Items:
3: Sets aperture positions (manually…? I wouldn’t f*** with this one prolly).
5: Manual RGB Gain
6: Manually sets focus position
8: “Test for offfset” option. Not sure what it does.
C: Some kind of Park to Zero Position calibration, gets stuck on endless loop.
F: Sets the drum diameter and focus elevation for specific drum (manually)
J: Not sure. Says the jumper is not in the right positions and stops
L:…..really weird stepper motor dance. goes the whole length back and forth indefinitely in little even spurts. had to just turn off the scanner.
K: Not sure what it is on the 5000, but on the 11000, this is for setting the drum zero position, which I believe is the drum line start point…
M: Some kind of motor calibration. “now we ramp spindle current” but nothing happens.
V: Shows lamp voltage
Period Next to Enter Key (only on keyboards with number pad): Crazy mega calibration. It went for over 24hours and I turned off the scanner.
I think it may be looking for certain targets etc somewhere on the drum and not finding them so it can’t complete. This one is especially interesting, but probably useless if we can't figure out what it's looking for.
If you open the firmware file in text editor, it shows this menu buried deep in the middle of it:
Scanmate 5000 monitor version 1.02.
Commands availible is :
Move Spindel Z/P/L/. 1
Adjust PMT Gain 2
Adjust Aperture 3
Choose Aperture 4
Adjust Gain constants 5
Calibrate Focus 6
Check Focus 7
Play with Offset values 8
Calibrate Apertures 9
Toggle Lamps 0
Make a ramp using the spindel current M
Make a ramp using the Gain, and Offset N
Output a byte to a port O
Input a byte from a port I
Output a word to a port Y
Input a word from a port X
Turn On SCSI S
Turn On SCSI in switch seek mode W
Test the palette ram A
Rotate Drum T
Enter Focus value manually F
Make spindel moves continously C
Set focus position to zero H
Test Barcode Circuit G
Show scanner options *
Show this help menu ?
Commands availible is :
Move Spindel Z/P/L/. 1
Adjust PMT Gain 2
Choose Aperture 4
Check Focus 7
Calibrate Apertures 9
Toggle Lamps 0
Turn On SCSI S
Turn On SCSI in switch seek mode W
Rotate Drum T
Set focus position to zero H
Test Barcode Circuit G
Show scanner options *
Show this help menu ?
Does anyone know how and why to use some of these things?
Scanmate 5000 Secret Service Menu Items:
3: Sets aperture positions (manually…? I wouldn’t f*** with this one prolly).
5: Manual RGB Gain
6: Manually sets focus position
8: “Test for offfset” option. Not sure what it does.
C: Some kind of Park to Zero Position calibration, gets stuck on endless loop.
F: Sets the drum diameter and focus elevation for specific drum (manually)
J: Not sure. Says the jumper is not in the right positions and stops
L:…..really weird stepper motor dance. goes the whole length back and forth indefinitely in little even spurts. had to just turn off the scanner.
K: Not sure what it is on the 5000, but on the 11000, this is for setting the drum zero position, which I believe is the drum line start point…
M: Some kind of motor calibration. “now we ramp spindle current” but nothing happens.
V: Shows lamp voltage
Period Next to Enter Key (only on keyboards with number pad): Crazy mega calibration. It went for over 24hours and I turned off the scanner.
I think it may be looking for certain targets etc somewhere on the drum and not finding them so it can’t complete. This one is especially interesting, but probably useless if we can't figure out what it's looking for.
If you open the firmware file in text editor, it shows this menu buried deep in the middle of it:
Scanmate 5000 monitor version 1.02.
Commands availible is :
Move Spindel Z/P/L/. 1
Adjust PMT Gain 2
Adjust Aperture 3
Choose Aperture 4
Adjust Gain constants 5
Calibrate Focus 6
Check Focus 7
Play with Offset values 8
Calibrate Apertures 9
Toggle Lamps 0
Make a ramp using the spindel current M
Make a ramp using the Gain, and Offset N
Output a byte to a port O
Input a byte from a port I
Output a word to a port Y
Input a word from a port X
Turn On SCSI S
Turn On SCSI in switch seek mode W
Test the palette ram A
Rotate Drum T
Enter Focus value manually F
Make spindel moves continously C
Set focus position to zero H
Test Barcode Circuit G
Show scanner options *
Show this help menu ?
Commands availible is :
Move Spindel Z/P/L/. 1
Adjust PMT Gain 2
Choose Aperture 4
Check Focus 7
Calibrate Apertures 9
Toggle Lamps 0
Turn On SCSI S
Turn On SCSI in switch seek mode W
Rotate Drum T
Set focus position to zero H
Test Barcode Circuit G
Show scanner options *
Show this help menu ?
Does anyone know how and why to use some of these things?
xanderrrrrr
Newbie
Let us know if it fits. Would make the job much easier indeed. This far I've used thin wires with hooks to measure each channel.
Other question I've always had related to this: what do the PMT Gain constraints adjustment really do, anyone knows more detail about it?
They do not follow the same "3 volt" PMT Gain rule, instead the voltages go "overboard" as you go bigger apertures when I measured voltages from the board on each channel. Seems like it's nearly impossible to adjust them right unless you have some exponential (graph-) table calculated for their exact values for each channel and aperture?
Voltage to the bulb is inconsistent. Try cleaning the leads that go to the bulb with contact cleaner and a metal brush, and replace the bulb of course. Replace the fuses, get an external fan for the bulb that’s more powerful and unplug the one that it’s using now. Unplug and replug everything on the board you can get your hands on— having good firm uncorroded connections is a mustHello, i'm having some weird lines on my scans. I have a SM11000 scanned with CQ on Win10. Mylar is new, and i don't know why i'm getting this lines. I attach you some photos of my negatives, wet mounted on the drum. Are they on the right position? Or must is flip 90º ? The lines appears mostly on dark areas.
Thank You
xanderrrrrr
Newbie
As far as noise goes, that has a lot to do with how you invert. I would strong recommend looking into negative lab pro. Generally use “basic” inversion algorithm and select linear or linear flat. Sometimes check the soft highlight button, or -5 white clip or black clip if you want something very flat to throw curves on in photoshop. If you’re outputting full contrast from color perfect, I wouldn’t. Watch my video. It’s low production value but the info is good.I was able to solve the problem.
The PC, SCSI card, and SCSI cable were not the cause.
I used a lens cleaner to wipe the lens in the position where the drum is set, and it worked beautifully.
Sometimes, even if the preview was successful, I would get a strip error.
That error also disappeared.
If you get "Error no.1473: Could not read from the scanner", just clean the lens instead of turning off the scanner or taking other violent measures.
If you encounter the same error in the future, try this. If you encounter similar errors in the future, try this.
nagya
Member
Hi guys,
I have a problem with my Scanmate 11000 scanner.
After a while, after about half an hour of scanning, the scanned images start to slide heavily in the purple direction. What could be the cause of this and how can I prevent it. Thanks in advance for any help.
I have a problem with my Scanmate 11000 scanner.
After a while, after about half an hour of scanning, the scanned images start to slide heavily in the purple direction. What could be the cause of this and how can I prevent it. Thanks in advance for any help.
monkeyfist
Established
Its probably your bulb, the color temperature might change when it gets warmer. Maybe try replacing it.Hi guys,
I have a problem with my Scanmate 11000 scanner.
After a while, after about half an hour of scanning, the scanned images start to slide heavily in the purple direction. What could be the cause of this and how can I prevent it. Thanks in advance for any help.
monkeyfist
Established
Utterly pointless software, inverting negs takes like 3 clicks in photoshop. Trying to automate it just leads to bad outcomes.As far as noise goes, that has a lot to do with how you invert. I would strong recommend looking into negative lab pro. Generally use “basic” inversion algorithm and select linear or linear flat. Sometimes check the soft highlight button, or -5 white clip or black clip if you want something very flat to throw curves on in photoshop. If you’re outputting full contrast from color perfect, I wouldn’t. Watch my video. It’s low production value but the info is good.
It also leads to people not understanding what they are doing, and in the mentality that there is some sort of "correct" output, meaning people wont print their images at all. Something that is a common in film photography nowadays. People just post stuff straight out of the scanner.
monkeyfist
Established
The service menu is documented in the field service manual.Hey guys, not sure if anyone has experience with the "hidden service menu" items in the service program... here's what I've found:
Scanmate 5000 Secret Service Menu Items:
3: Sets aperture positions (manually…? I wouldn’t f*** with this one prolly).
5: Manual RGB Gain
6: Manually sets focus position
8: “Test for offfset” option. Not sure what it does.
C: Some kind of Park to Zero Position calibration, gets stuck on endless loop.
F: Sets the drum diameter and focus elevation for specific drum (manually)
J: Not sure. Says the jumper is not in the right positions and stops
L:…..really weird stepper motor dance. goes the whole length back and forth indefinitely in little even spurts. had to just turn off the scanner.
K: Not sure what it is on the 5000, but on the 11000, this is for setting the drum zero position, which I believe is the drum line start point…
M: Some kind of motor calibration. “now we ramp spindle current” but nothing happens.
V: Shows lamp voltage
Period Next to Enter Key (only on keyboards with number pad): Crazy mega calibration. It went for over 24hours and I turned off the scanner.
I think it may be looking for certain targets etc somewhere on the drum and not finding them so it can’t complete. This one is especially interesting, but probably useless if we can't figure out what it's looking for.
If you open the firmware file in text editor, it shows this menu buried deep in the middle of it:
Scanmate 5000 monitor version 1.02.
Commands availible is :
Move Spindel Z/P/L/. 1
Adjust PMT Gain 2
Adjust Aperture 3
Choose Aperture 4
Adjust Gain constants 5
Calibrate Focus 6
Check Focus 7
Play with Offset values 8
Calibrate Apertures 9
Toggle Lamps 0
Make a ramp using the spindel current M
Make a ramp using the Gain, and Offset N
Output a byte to a port O
Input a byte from a port I
Output a word to a port Y
Input a word from a port X
Turn On SCSI S
Turn On SCSI in switch seek mode W
Test the palette ram A
Rotate Drum T
Enter Focus value manually F
Make spindel moves continously C
Set focus position to zero H
Test Barcode Circuit G
Show scanner options *
Show this help menu ?
Commands availible is :
Move Spindel Z/P/L/. 1
Adjust PMT Gain 2
Choose Aperture 4
Check Focus 7
Calibrate Apertures 9
Toggle Lamps 0
Turn On SCSI S
Turn On SCSI in switch seek mode W
Rotate Drum T
Set focus position to zero H
Test Barcode Circuit G
Show scanner options *
Show this help menu ?
Does anyone know how and why to use some of these things?
monkeyfist
Established
It seems the most problematic part of the scanner is actually the relay board, i am hearig the clicking sound more and more often . The system is collapsing even after some aperture calibration, wb calibration, or a simple scan/preview.
maybe the roots of all problem is the driver board/power supply.
what do you think?
Might be, i actually have a problem where the stepper motor no longer produces enough power and gets stuck.
I tried replacing the stepper motor driver, was a wrong move and currently just trying to fix what i broke while doing it while replacing it with a new driver as i suspect that the first one that i put there was a fake chip.
A fan was disconnected that cools down the power board & stepper driver, so i though maybe my stepper driver had died or something. I did measure it was getting the 40v on the motor input. But not sure. Would be shame if i cant get this to work.
monkeyfist
Established
Lols it works, #diy.Might be, i actually have a problem where the stepper motor no longer produces enough power and gets stuck.
I tried replacing the stepper motor driver, was a wrong move and currently just trying to fix what i broke while doing it while replacing it with a new driver as i suspect that the first one that i put there was a fake chip.
A fan was disconnected that cools down the power board & stepper driver, so i though maybe my stepper driver had died or something. I did measure it was getting the 40v on the motor input. But not sure. Would be shame if i cant get this to work.
I tore so many traces off the board while removing that driver chip the second time.
But it seem the problem actually was in the stepper driver chip.
Now i just have a problem of how to heatsink that chip, it would require soldering the heatsinks to the ground pins.. and that seems tricky.
Just slapping few heatsink on top of it probably does not work.
So happy with this, been trying to ignore my non working SM11000 so i would not have to face the possibility of it being a big piece of junk metal.
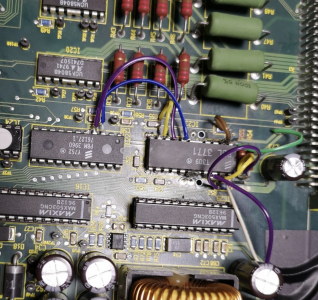
If anyone ever has to do this, the layout follows the suggested diagram in the datasheet of the PBL3771.
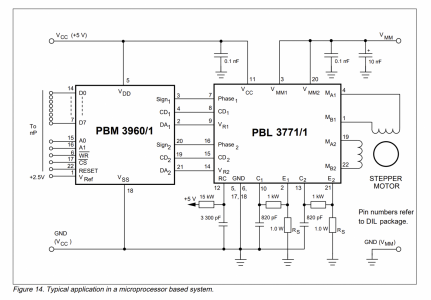
Last edited:
RobertRobson
Newbie
I am preparing for a court hearing for compensation from the courier for damage to the Scanview Scanmate 5000 scanner and I cannot find a current advertisement anywhere with a price to present in court. Do any of you know what the value of this scanner might be today?
I think the only Ebay reference I found was yours.
This company uses one for film scanning:
Maybe you could ask them, also point to your for-parts auction.
I'll check around.
RobertRobson
Newbie
Thanks, I called them but they don't know how much is it worth. Also they use different drum scanner now but they are keeping scanmate 5000. Yes the listing on ebay is mine, In my opinion judging by interest on ebay working unit could be worth 2800-3500Euro. But views of my lisitng and watchers is not a solid proof.
Share:
-
This site uses cookies to help personalise content, tailor your experience and to keep you logged in if you register.
By continuing to use this site, you are consenting to our use of cookies.